Job Meetings
For the project to succeed, key personnel will meet on at least two occasions before work begins on the project, often during execution of the project and at least once at the conclusion. These personnel are the Project Manager, the Building Manager (these two positions may be held by the same person), the Building Engineer, whose role in the project may be significant, the contractor’s Project Manager, the contractor’s Operations Manager, the Job Foreman, or Foremen and the Consultant, if one has been hired. The meetings that these personnel will participate in are the Bidders Conference, the Pre-Construction Meeting, Progress Meetings and Site Visits, regular Telephone Conferences and a meeting at the end of the project to close it out.
The Bidders Conference
The Bidder’s conference, which will take place on the site, is an aspect of the Bidding Process. It begins with a review of the project by going through all aspects of the Statement of Work and reviewing the specifications. It continues with walking around the building with all the bidders and taking them to the roof. There is a tendency for individuals, pairs and smaller groups to separate from the others during the walk-around. Participants should stay together so that all can benefit from the discussions that anyone initiates. Any questions that arise should be answered for all.
Bidders Meeting Example Agenda
This outline served as the agenda for a bidder’s conference. It was used by the consultant (JVS Building Services, LLC) to conduct the meeting. It included 3D representations of the building and photographs as well as bullet points intended to make the bidders familiar with the work areas, nomenclature, services and other elements of the building and the Statement Of Work.
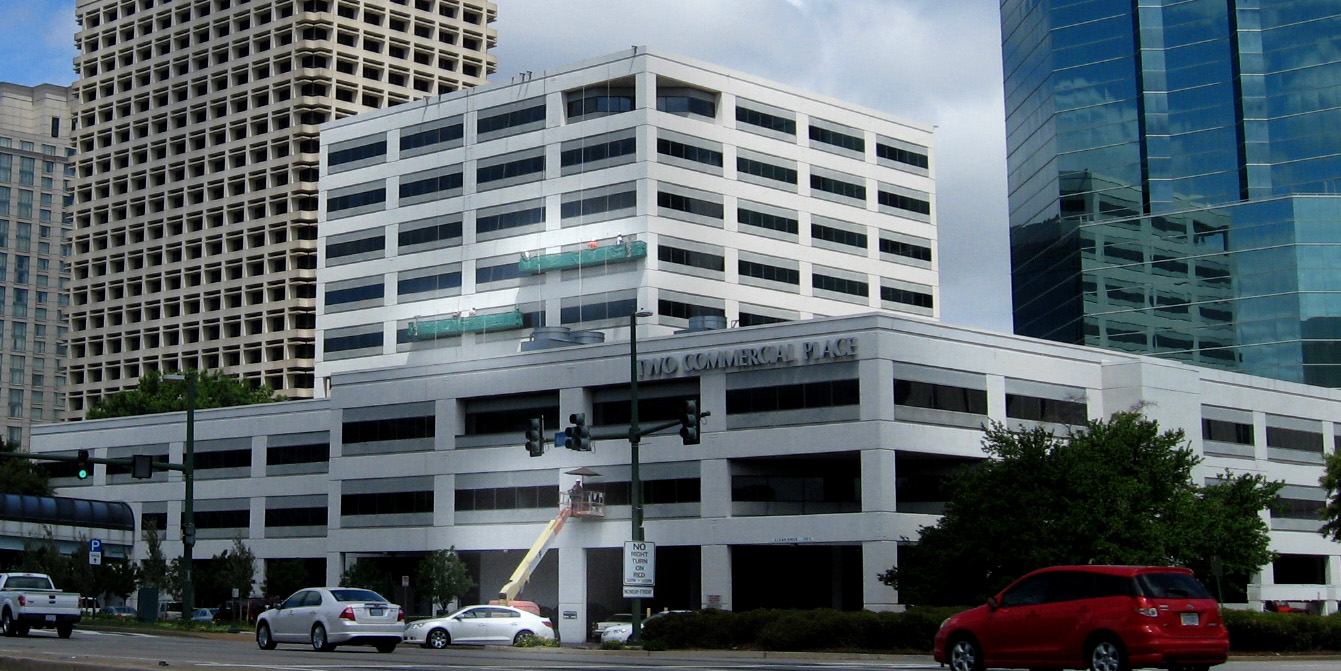
Pre Construction Meeting
This may be the most important event of the project because this is the moment when it is formally determined that all the preparations are complete. The Statement of Work and the specifications will have thoroughly described the work and they will have stated many requirements but they are not a set of instructions. How the project will be conducted is, in many significant ways, up to the contractor. His readiness will be established during this meeting.
This outline for a pre-construction meeting recently conducted for a 360,000 square foot pre-cast concrete office building illustrates why a review is necessary before the start of restoration operations:
1 Scope of Work and Schedule of Values
1.1 Any Questions on the Scope of Work? Have the parties all read it?
1.2 Any Questions on the Schedule of Values and how it’s to be used for invoicing?
2 Production Schedule
2.1 What is the order of work? (Refer to Sect. 3 of the SOW)
2.2 Duration, Milestones
2.3 Effect on Tenants and Building Operations
2.3.1 Are the impactful events on the schedule? Building manager needs to know beforehand
3 Production Issues
3.1 Gaskets and Wet Seals
3.1.1 Examples or acceptable and unacceptable gaskets will be posted at JVSBS.com
3.2 Are Weather Contingencies in the schedule? (“X” number of days per month based on historical data)
3.3 Current sealant location from face of frame:
3.3.1 makes extraction of old sealant difficult
3.3.2 temptation to skin over greater
3.3.2.1 Owner’s rep (building engineer or Consultant) needs to check
3.4 Weeps
3.4.1 Ops Manager and foreman are to continually remind subordinates and crew about the weeps (some, even most could be closed without diligence)
3.4.2 Owner reps need to check
3.4.3 What weep has been selected to meet the requirement in sect 2.1.1
3.4.3.1 “Weeps, with screens or mesh, designed specifically for the purpose are to be installed at the intersections of vertical joints with horizontal joints where needed to drain the wall cavities.”
3.4.3.2 Where will they be placed?
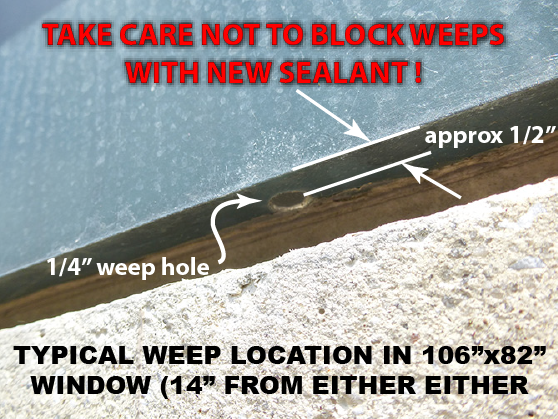
3.5 Where will lifts be used? Can the surfaces at those locations support the weight?
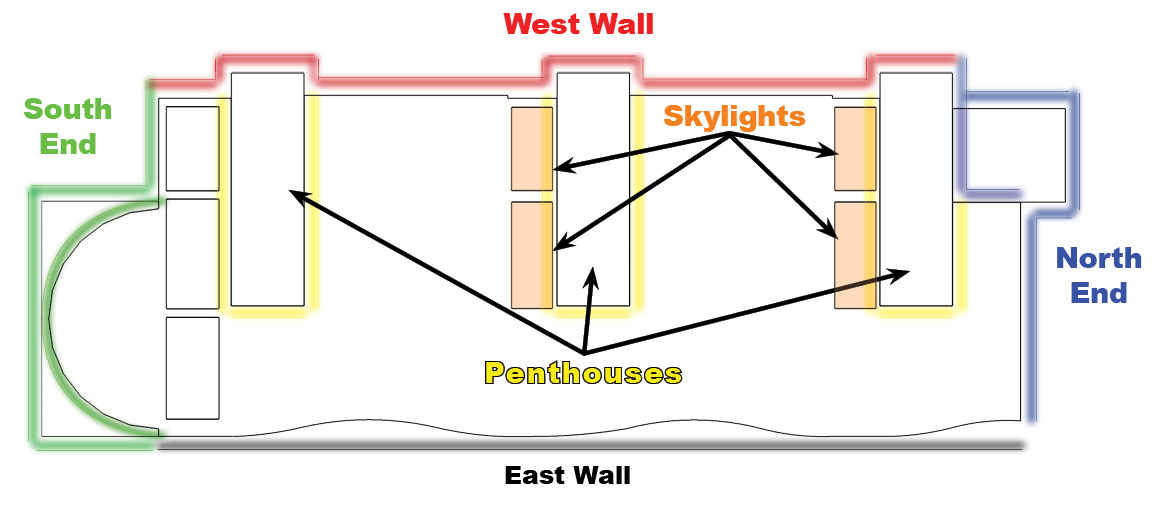
4 Materials
4.1 Are there any changes in the materials to be used from those called for in the SOW
4.1.1 Sealant
4.1.2 Window Frame Cleaning Agent
4.1.3 Window Frame Sealer
4.1.4 Window Restoration System
4.1.5 (alternate for the waterproofing material was not allowed)
5 Submittals / Submissions
5.1 only for materials that are different than recommended
5.2 provide statement that Dow’s “Contractor’s Guide” has been distributed to all crew members
5.3 Is conducting the safety survey on the production schedule? A statement to that effect is called for.
6 Power & Water
6.1 What steps have been taken for power hook-up? Where are the water connections?
6.2 Has the insurance certificate been provided?
6.3 Where is the contractor to locate their storage trailer?
7 Warranties
7.1 What has been done or and needs to be done to secure manufacturer’s warranties?
7.1.1 sealant
7.1.1.1 Conduct field adhesion tests, in accordance with the sealant manufacturer’s guidelines, of each joint type:
7.1.1.1.1 Concrete Joints (1.1.1.1), Perimeter Joints (1.1.1.2) and Glazing Joints (1.1.1.3).
7.1.1.1.2 At least two tests of each joint type are to be completed in each wall type on each area of work defined in Section 4 of the Statement of Work.
7.1.2 Window Restoration system
7.1.3 Waterproofing
8 Quality Control / Assurance
8.1 does the contractor have questions about the sealant specification
8.2 Are probes to be provided to the sealant installers and inspectors to check sealant adhesion?
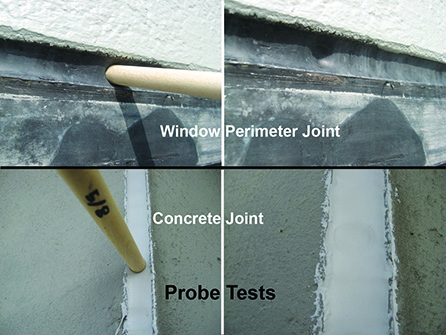
8.4 Is the building engineer or other owner’s representative qualified to point out flaws or defects?
8.5 adhesion test reports are to be submitted to the Consultant
Progress Meetings
Throughout execution of the project it is prudent, at least, to check on the work. There are contractors who are so good at what they do and so diligent at maintaining quality and production schedules that owners can let them go without checks. The trouble is, at any given time on any job you can’t know if your contractor is one of them. Owners and managers of restorations projects, who have decided to do what is always done in new construction, which is to inspect the work as it progresses, will expect to see reports that inform them of the status of the project, such as this one:
December 13, 2014
re: Dec. 11, 2014 Site Visit
I visited the site yesterday to check on the project. The work currently underway is sealant restoration on the East Wall and the North End of the building. Work on the East Wall was being done from two aerial lifts manned by Al Whitely and Howard Tabor. Eddy Jefferson and Frank Sturgis were working from a swing stage scaffold on the west end of the North Wall. The following conditions were observed and questions answered or raised:
1. I went up in one of the lifts with Al, the project foreman. I performed an adhesion test on a vertical joint between precast panels. The material was fully cured and properly tooled. The material adhesion was good. The depth of the joint I tested was greater than it should have been and I pointed that out to Al. The joint width to depth ratio should be 2:1 where the joint width is less than 1”. The ratio of the joint I tested, which was about 1/2” wide, was closer to 1:1. Also, more of the old material should have been removed. The effect of leaving an excess amount of the original material did not result in a failed adhesion test or an unacceptable joint but more of the old material could, and should have been removed.
2. Al then showed me a representative window perimeter joint. These are the joints identified in section 2.1.3 of the Scope of Work. The contractor’s work on these joints needs to be corrected in multiple, if not all, locations and the correct methods must be consistently applied throughout the remainder of the building. Addenda 1 of the Scope of Work indicates which joints are to be restored as well as the joint type. Section 18 on Sheet 8, for example, shows that a butt joint is be installed between the precast concrete and the curtain wall. The new joint, as shown in the figure on the next page, is a fillet joint, which will serve to close the space behind the joint but it is not the correct joint type. Direction needs to be provided to the contractor on which joints, if any, need to be re-installed.
3. Joint tooling should be improved. Where the proper type of joint (as described in item 2) is installed the detrimental aesthetic effect of poor joint lines may be alleviated, however, there are indications that joint tooling techniques are not uniformly good.
4. Another Masterprotect H1000 waterproofing sample should be installed and tested to ensure that the proper application technique is being used. Although the sample the contractor installed at ground level on the west end of the North Wall does repel water with an optimal application technique the result could possibly be improved. I recommend a BASF technical rep or another experienced applicator be tasked to install another sample on a properly prepared area. The technique should be documented so that it can be duplicated by the contractor.
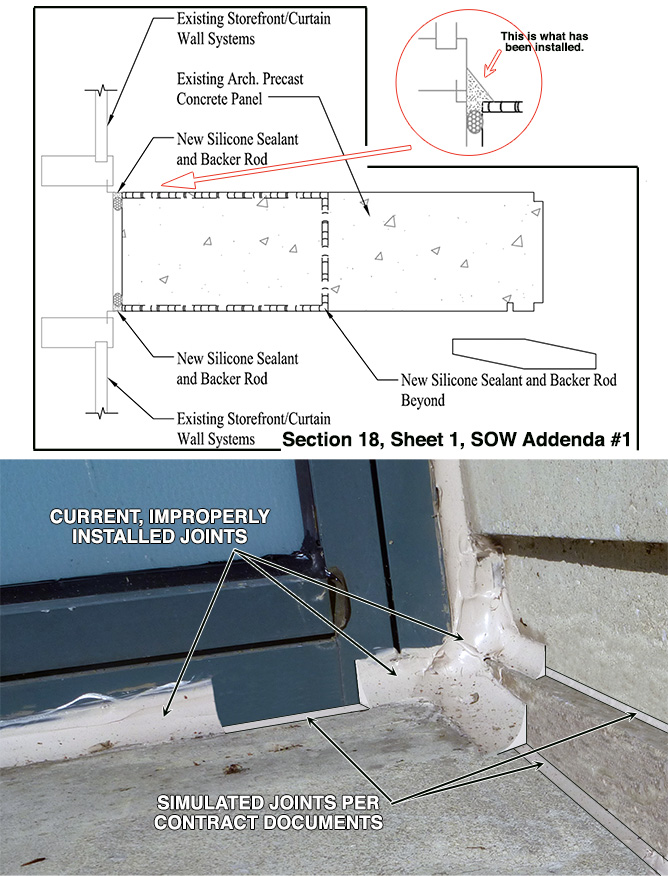
5. I examined a significant number of window gaskets on the East Wall and on the North Wall and did not see any that were in need of replacement. The crew has found some and installed wet seals where needed. The condition that has made that necessary in most cases has been loose gaskets rather than deterioration. Al said that he’s keeping a count of what’s been done. This is needed in order to establish the final, billable amount for this work item.
6. The point about the fillet joints was discussed with Mike Keasey Friday morning so that he could inform the installers before any more improper joint types are installed.
7. As mentioned, some of the existing work should be corrected. How much and the criteria by which the judgment is made as to which joints are corrected needs to be determined.
8. A thorough review of the Scope of Work including the Addenda drawings should be conducted with the installers. They must be aware of details and the requirements in order to meet them.
Rob Crimmins, JVS Building Services
Project Close-out
If a consultant was hired to help oversee the project he or she will have kept track of the progress and quality of the work. That function could have also been accomplished by the owner’s Project Manger, the building manager or the building engineer. Without any of those individuals assigned to the task it will have been left to the contractor. Regardless of who does it someone has to verify or attest to completion of the work so final payments, including retained amounts, can be made and warranties issued.
If the contractor’s notice that work is complete is all that’s required a meeting isn’t necessary. If the owner or his representative is diligent assurance that the work is complete will be sought. This is typically done by inspecting the work and creating a list of all unfinished or incomplete work and all conditions that need to be corrected. The “Punch List” is the work product of the inspection.
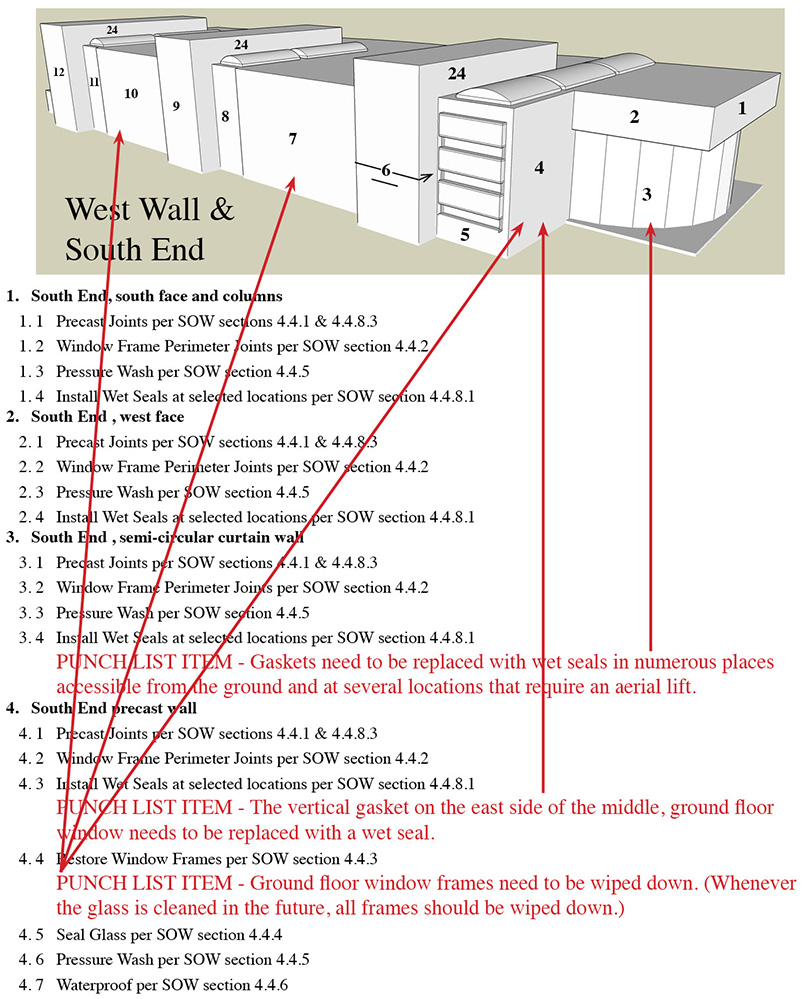
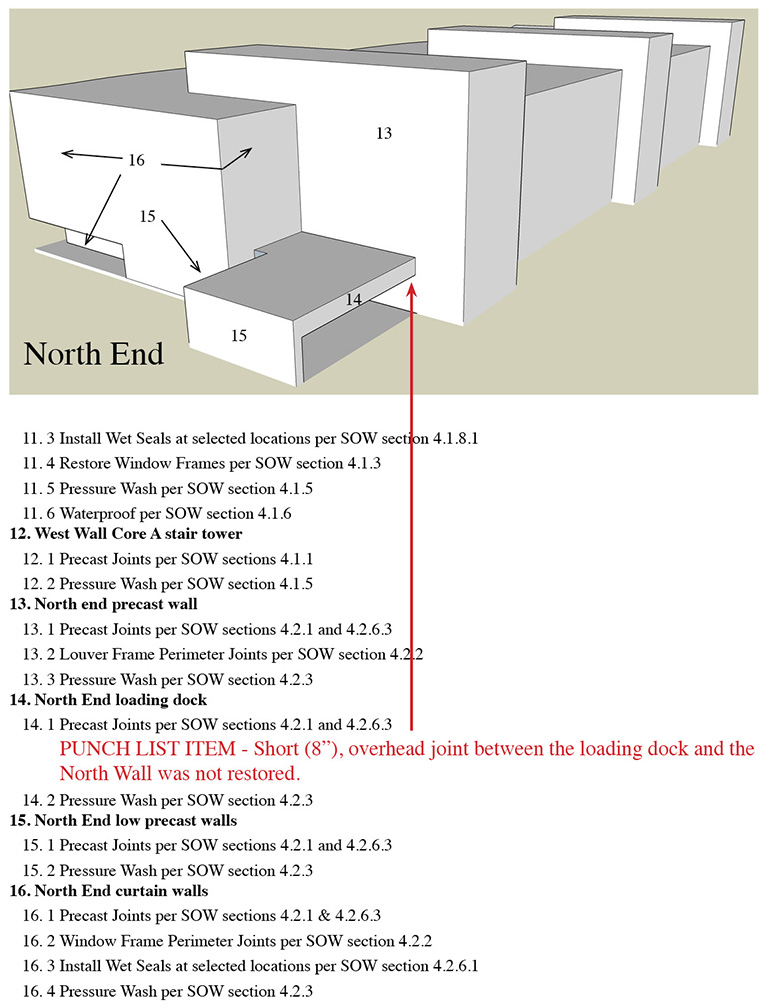
The following example uses a rough 3 dimensional representation of the building and references to the Statement of Work to clearly indicate where work still remains. It should be noted that in restorations projects waiting until the end of the project to do the first punch list creates problems. Returning to a wall after the work platforms have moved will call for a rigging exercise that would not have been needed if the work had been inspected before the equipment was relocated. To avoid such waste inspections should be included in the production schedule.
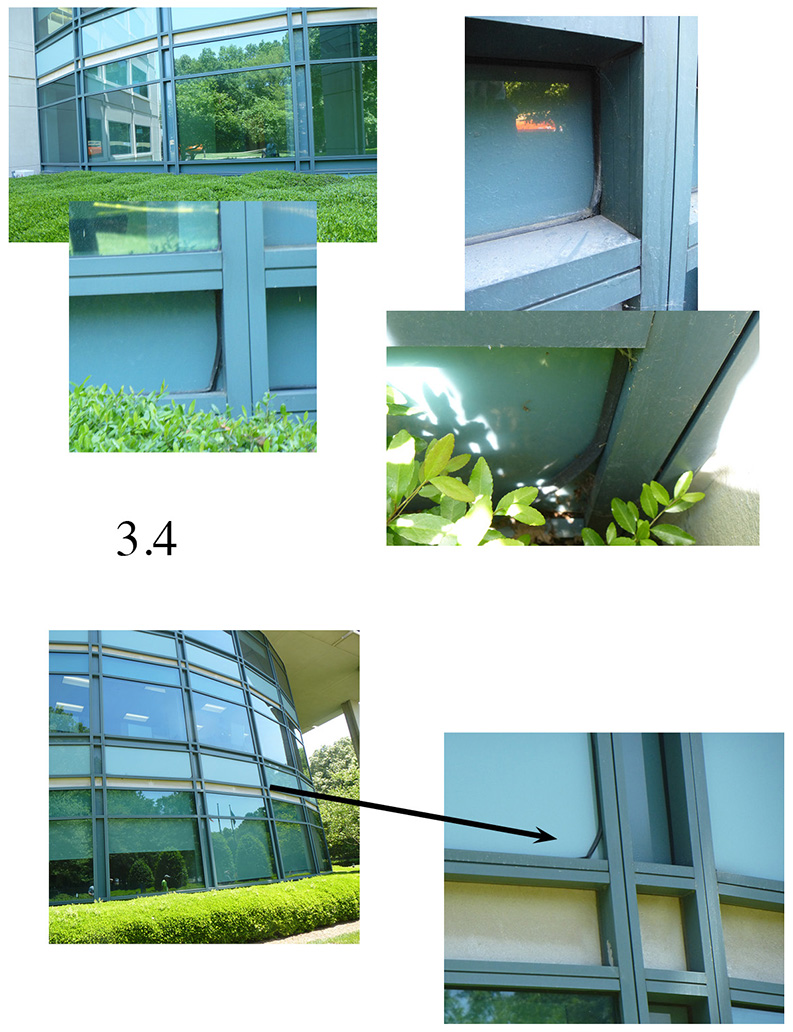
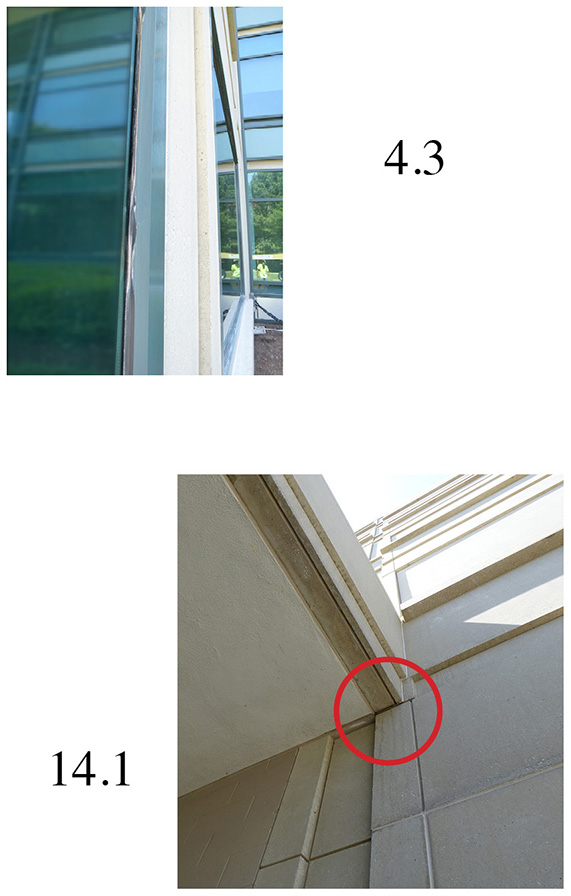
Rough Model of the Concourse at Northampton – Norfolk, Virginia
Scroll to zoom in on the 3D model and drag to orbit about it. Drag cursor + SHIFT to pan