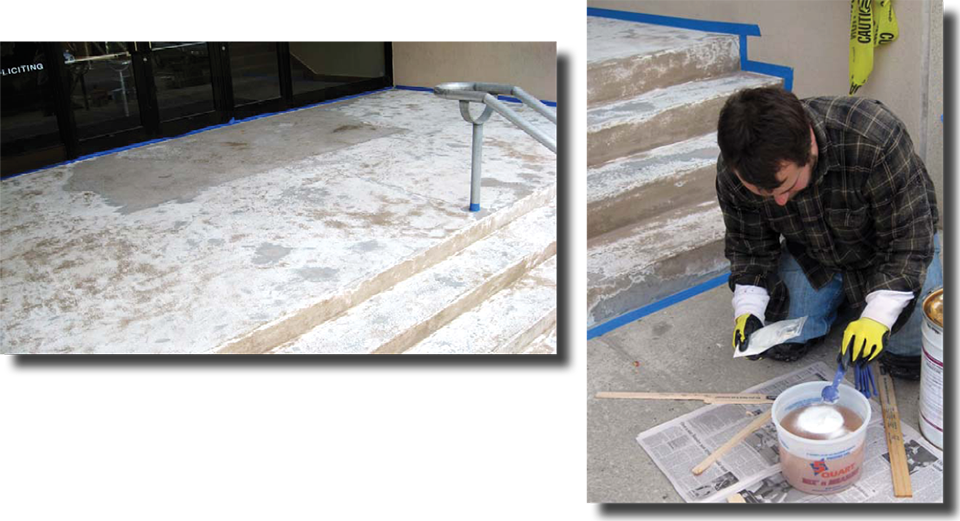
This report details the process of preparing the surface of a 517 square foot entry plaza and applying polymethyl methacrylate under the supervision of the Soprema Corporation technical representative. Because PMMA is a catalyzed system it cures very rapidly. This makes it a good solution for areas that have to be back in service quickly, which was the case here. The work on this plaza was completed over a weekend so the building entrance adjacent to it was available for use Monday morning. The catalyzed material generates heat as it cures so it can be applied when the ambient temperature is low. This project was completed in Philadelphia in the winter so water based products and any other that is susceptible to freezing was not an option.
We got started on scarifying the surface, which turned out to be very difficult, Friday night at 6 O’clock. It took until 3 AM to remove enough material. There were multiple layers, as many as six, one grey, two beige and three brown, but no fewer than four. In part of the area under the mat all layers except the original grey could be peeled up. Everywhere else the material was ground to dust.
In order to finish in time for application of the material on Saturday we didn’t scarify the entire surface to the concrete. We were able get that far in the area in front of the double doors where the mat had been. And there were a number of other spots where bare concrete was exposed but the rest of the final surface was well adhered, previously applied material. We applied the diamond cup wheels to every inch and all the way to each edge. When we finished nothing that wasn’t well adhered remained.
The primer and the textured finish were applied by or under the supervision of the Soprema technical representative, Jeff Demeter. He closely examined the surface before the application of primer and while the primer was curing. His opinion of the substrate was that it was good but he reminded me that it was not ideal, repeating that the ideal is clean concrete. During the cure he looked for “bubbles” which would indicate moisture. None were seen. Moisture on or in the substrate precludes granting a warranty so it was important that the fact that there was none was established.
Primer was applied and cured followed by the “textured finish”. At the conclusion of the textured finish application and once it was almost completely cured, Jeff left. Cure was complete in less then an hour. At that point I was able to walk on the surface to do some touch up at the edges and in a few areas in the field. Working with it at that point I discovered how tough the material is. By then, when the cure was complete, the material was very hard and very tough. It will wear extremely well. The rollers and roller handles and the remaining materials were left for Rich Streeper and I’ll leave the colored base with him too but I don’t think it will ever be needed.
Soprema, Alsan RS is a PMMA (Polmethyl methylarcylate), liquid system. It is extremely tough, hydrophobic and encapsulating. When properly mixed and applied to clean, “virgin” concrete it will probably last for many decades. Twenty year warranties from Soprema may be common. The deck at 150 Monument was not ideal, nor were the project conditions, although the time constraints is why the PMMA, liquid system was chosen. The market for the product is specifically for locations that can’t be shut down while products cure. Here’s a link to a good article on how it’s used and by who: http://www.plantservices.com/articles/2009/026.html. It’s written for property managers.
The discussions about the warranty are important and all the conditions will be taken into account. I think what you have now will last indefinitely but Soprema knows exactly what the conditions were and how the final coat will be applied. (Based on my training I assume they have confidence in how that step will be accomplished.) They will establish the warranty period for the material and I’ll work with them as needed to get the warranty to you if they agree to offer one.
The failure to receive the color notwithstanding Soprema has proven to be an outstanding partner. Their sales representative, Rick Brehm, was very helpful working with us at the project site with you and with the material distributor. He offered complete support to me as I prepared to take on this new market. Jeff Demeter was very knowledgeable and “hands on”. He worked with us and ahead of us through the whole process offering everything he could.
The distributor, TB Philly, Inc., Phoenixville, PA did a great job too. This was the first time they had dealt with these materials. It was complicated and they performed in an exemplary fashion.
As discussed I’ll come on Sunday, November 28th to apply the top, colored coat.
Alsan RS may be able to take it but I recommend not using a solid mat again. The one that was there held water or trapped moisture that was coming up from the ground through the concrete. You can see from the picture that area was different than the rest of the deck and the damage to the old coating much more extreme. An open mat of some kind or one of breathable material would be better.
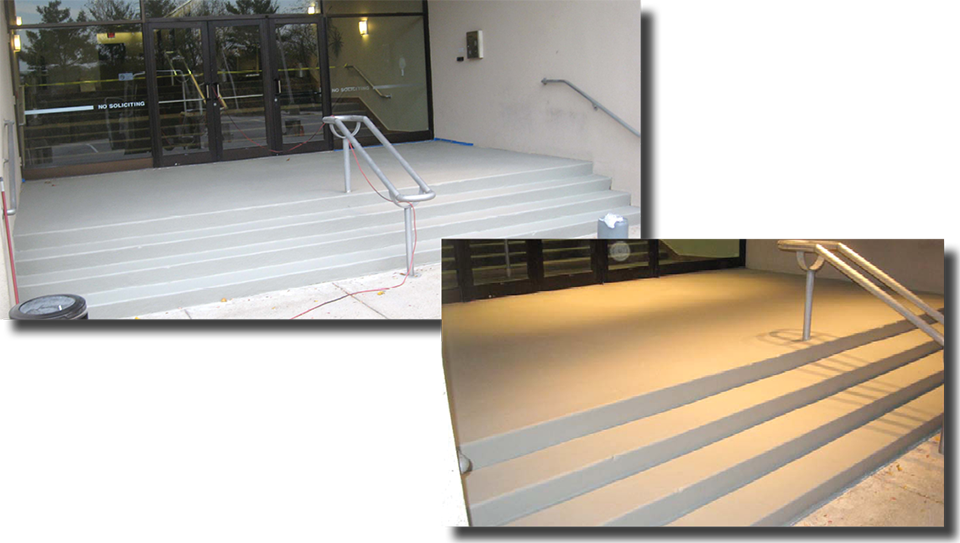